Good evening everyone,
I have come across a great problem (it's great only because I am glad to be at this juncture of the restoration).
How have you all found the most accurate and efficient way to match a patch panel to fit into the cut out portion of bad metal. I cut out a general patch from the repro fender but having some trouble figuring out whether I should cut out the original fender to match the patch or keep cutting away at the patch until it fits into the cut out.
I have come across a great problem (it's great only because I am glad to be at this juncture of the restoration).
How have you all found the most accurate and efficient way to match a patch panel to fit into the cut out portion of bad metal. I cut out a general patch from the repro fender but having some trouble figuring out whether I should cut out the original fender to match the patch or keep cutting away at the patch until it fits into the cut out.
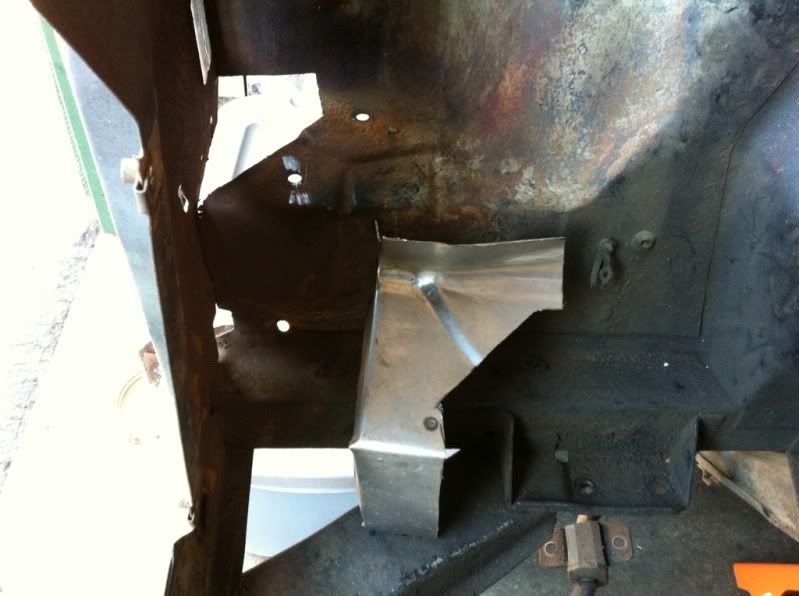