Nothing is ever easy. I am in need of a special type of fastener that, to date, I have been unable to find. I'm to the point I might just invest in a 3D printer and make my own!
What I want is a double ended stud where one end is conventional threads and the other has a press fit/locking end to secure a plastic piece to the surface of another panel. Basically, I'm looking to tightly secure a shallow trim piece (<1/4" thickness) to the surface of a panel with a hidden fastener. Something like this would be perfect.
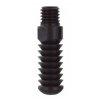
The base piece is very thick so I cannot use something that would pass-through from the back side. Has to be done from the surface. I could machine a pocket in the primary piece into which I could thread the pin and have only the interference portion above the panel surface to mate with the trim. Problem is the only thing I have found so far like this is in the medical field and I haven't been able to find a source from which to buy for less than a million dollars.
My other idea (born from my redneck heritage) is to just cut the head of a bolt or screw and thread it in and press the trim over the headless end. The trim is a flexible rubber like plastic so this will likely work but if anyone is familiar with a fastener made for this type of application (surface pairing of two pieces)...and there has to be one...please give me some direction. Ideal sizing would be something in the neighborhood of 1/4" max diameter with a interference shaft length above the panel surface of 3/16". I could always also screw the threaded end into the trim and use a longer press fit shaft to go into the base material. this might actually be the better way to go now that I type it...
What I want is a double ended stud where one end is conventional threads and the other has a press fit/locking end to secure a plastic piece to the surface of another panel. Basically, I'm looking to tightly secure a shallow trim piece (<1/4" thickness) to the surface of a panel with a hidden fastener. Something like this would be perfect.
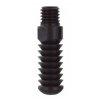
The base piece is very thick so I cannot use something that would pass-through from the back side. Has to be done from the surface. I could machine a pocket in the primary piece into which I could thread the pin and have only the interference portion above the panel surface to mate with the trim. Problem is the only thing I have found so far like this is in the medical field and I haven't been able to find a source from which to buy for less than a million dollars.
My other idea (born from my redneck heritage) is to just cut the head of a bolt or screw and thread it in and press the trim over the headless end. The trim is a flexible rubber like plastic so this will likely work but if anyone is familiar with a fastener made for this type of application (surface pairing of two pieces)...and there has to be one...please give me some direction. Ideal sizing would be something in the neighborhood of 1/4" max diameter with a interference shaft length above the panel surface of 3/16". I could always also screw the threaded end into the trim and use a longer press fit shaft to go into the base material. this might actually be the better way to go now that I type it...
Last edited: