janschutz
Corn Hauler
Last year was good for getting rid of stuff, I went through 11 boxes and repurposed or fixed a lot of stuff.
I used some foam board to cut out with my work's laser to cut out a prototype paint can holder. I am currently cutting out the pieces for the real shelf out of some scrap 1/2" plywood. This will be going on my cleat wall in the maintenance barn.
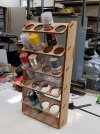
I used some foam board to cut out with my work's laser to cut out a prototype paint can holder. I am currently cutting out the pieces for the real shelf out of some scrap 1/2" plywood. This will be going on my cleat wall in the maintenance barn.
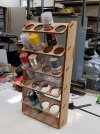