I've always like the Ron Morris motor mounts and everyone else seems to as well, but I just didn't want to fork out $225 for about $20 in steel and $20 in bushings. I also am not a fan of the urethane bushings used, so my design will utilize stock rubber bushings made for the rear shackles of our cars. If I find that the rubber wears too quickly or the bolt pushed through the rubber, I can always buy the urethane shackle bushings to replace these rubber ones.
Initially I wanted to mimic the Ron Morris design but I wasn't a fan of the motor mounts being of 3 sections: the top plate, the intermediate section consisting of a top plate/angled plate/bushing housing, and the shock tower brackets. I wanted to combine the top plate and bushing housing into one, similar to the TCP mounts but I didn't want to lose the option of sliding the engine back (which is the reason for these mounts). I decided to try to make the top plate have long slotted holes and make the front to back motor adjustments though those two bolts that go into the engine. The oil filter is in the way up front on the drivers side and there is a plug in the way on the front passenger side. Because of this, I conceded to try and mimic the Ron Morris mounts. RyanG85 and 65Fast helped with a getting me some measurements of their RM mounts, just for sanity checks to make sure I'm not way out of whack. Thanks guys!
Here is what I have to take measurements from:
I used a caliper to take the measurements and below is what I came up with, drawn in Autocad:
Using these dimensions, I drew up the shock tower brackets. I used 1/2" edge distance from the edge of bolt hole to edge of plate for 7/16" bolt holes (two for shock tower) and 5/8" edge distance for 1/2" bolt holes. I wanted to keep the cutting easy, so the top edge is flat. Due to the different edge distances from the two different bolt hole sizes, the hole centerlines are not inline as seen below:
The above drawing started out with pointed and square corners, and then I started drawing up circles that would be trimmed to make the rounded edges. Below is the result:
I also put in the bushing carrier and started to draw up the top plate. Below is next steps completed:
I established the bolt hole locations for the intermediate plate. The long line going at an angle is 45° from the centerline of the bushing. Its just a reference point so that the angle of the plate welded to the bushing housing doesn't get greater than that angle. The next step was finalizing the intermediate plate as seen below:
The final step was to draw in the angled plate that connects the bushing housing to the intermediate top plate.
The above view is the completed side view of the motor mount assembly. This weekend I plan on drawing up the top view showing the width of the bushing, bushing housing, and details of the top plate and intermediate plate. I'm waiting on my rubber shackle bushings to come in the mail. When finalized, I will break up each part so that they can be transferred to steel plate to be cut. I plan on dimensioning everything and posting it on here so that other DIY guys can mimic my mounts...at your own risk of course :scar More to come later!
Oh, forgot to mention that when finished I'll be transferring these drawings onto cardboard for mock-up rather than going straight to cutting steel. Just in case something is off! :lol
Initially I wanted to mimic the Ron Morris design but I wasn't a fan of the motor mounts being of 3 sections: the top plate, the intermediate section consisting of a top plate/angled plate/bushing housing, and the shock tower brackets. I wanted to combine the top plate and bushing housing into one, similar to the TCP mounts but I didn't want to lose the option of sliding the engine back (which is the reason for these mounts). I decided to try to make the top plate have long slotted holes and make the front to back motor adjustments though those two bolts that go into the engine. The oil filter is in the way up front on the drivers side and there is a plug in the way on the front passenger side. Because of this, I conceded to try and mimic the Ron Morris mounts. RyanG85 and 65Fast helped with a getting me some measurements of their RM mounts, just for sanity checks to make sure I'm not way out of whack. Thanks guys!
Here is what I have to take measurements from:
I used a caliper to take the measurements and below is what I came up with, drawn in Autocad:
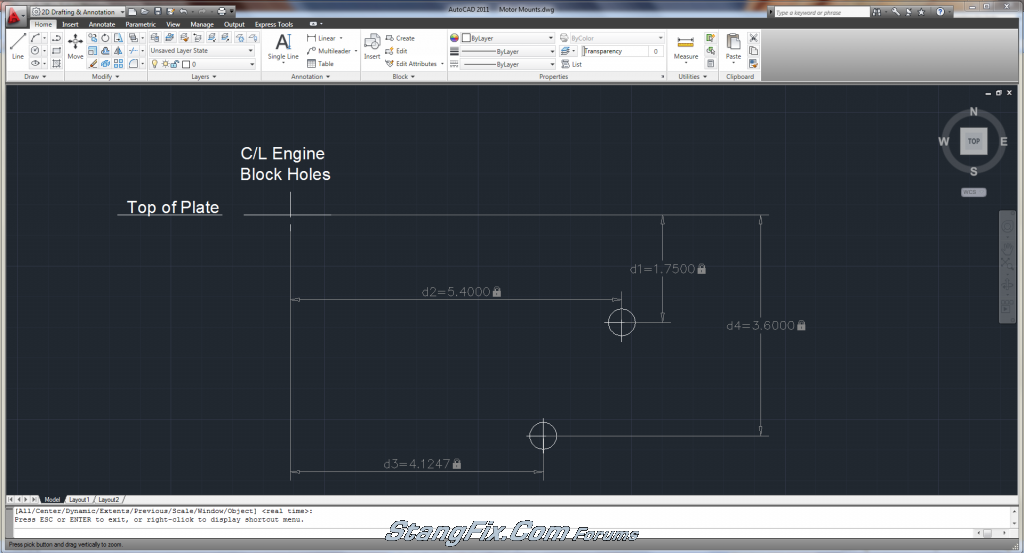
Using these dimensions, I drew up the shock tower brackets. I used 1/2" edge distance from the edge of bolt hole to edge of plate for 7/16" bolt holes (two for shock tower) and 5/8" edge distance for 1/2" bolt holes. I wanted to keep the cutting easy, so the top edge is flat. Due to the different edge distances from the two different bolt hole sizes, the hole centerlines are not inline as seen below:

The above drawing started out with pointed and square corners, and then I started drawing up circles that would be trimmed to make the rounded edges. Below is the result:
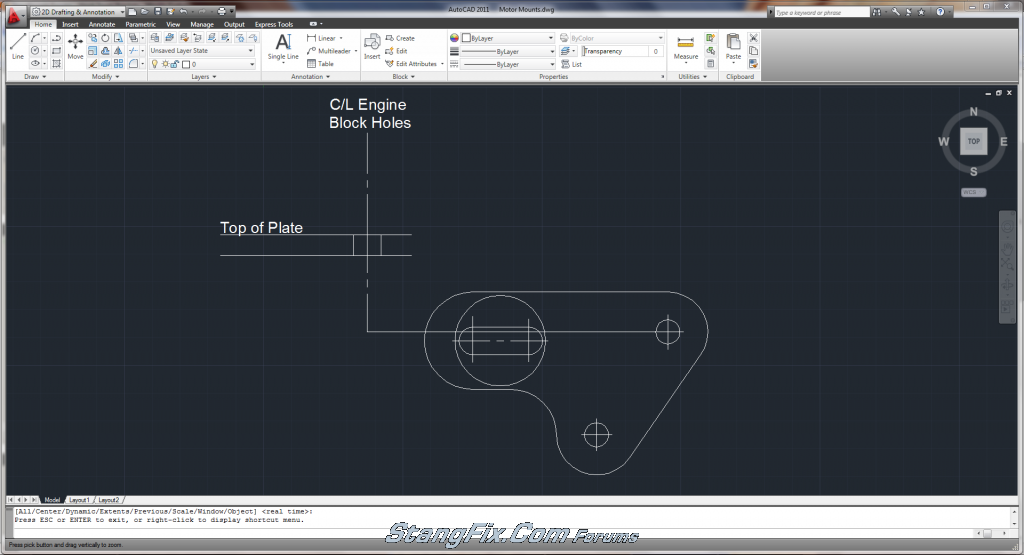
I also put in the bushing carrier and started to draw up the top plate. Below is next steps completed:
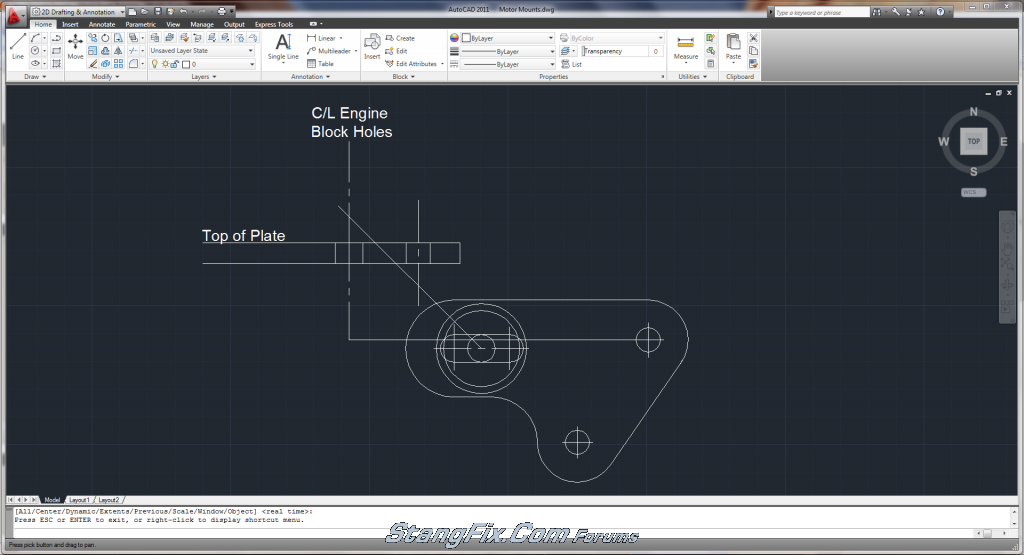
I established the bolt hole locations for the intermediate plate. The long line going at an angle is 45° from the centerline of the bushing. Its just a reference point so that the angle of the plate welded to the bushing housing doesn't get greater than that angle. The next step was finalizing the intermediate plate as seen below:
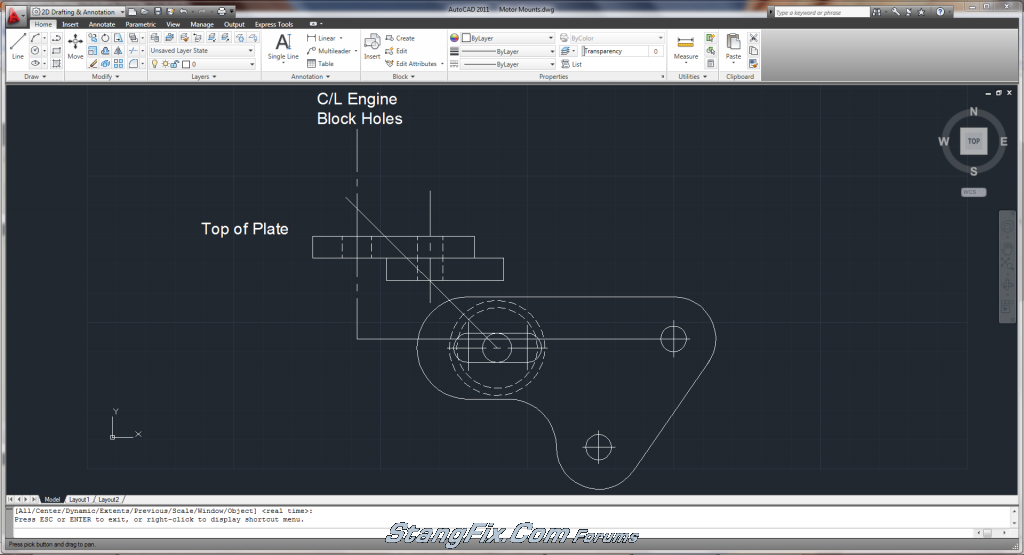
The final step was to draw in the angled plate that connects the bushing housing to the intermediate top plate.
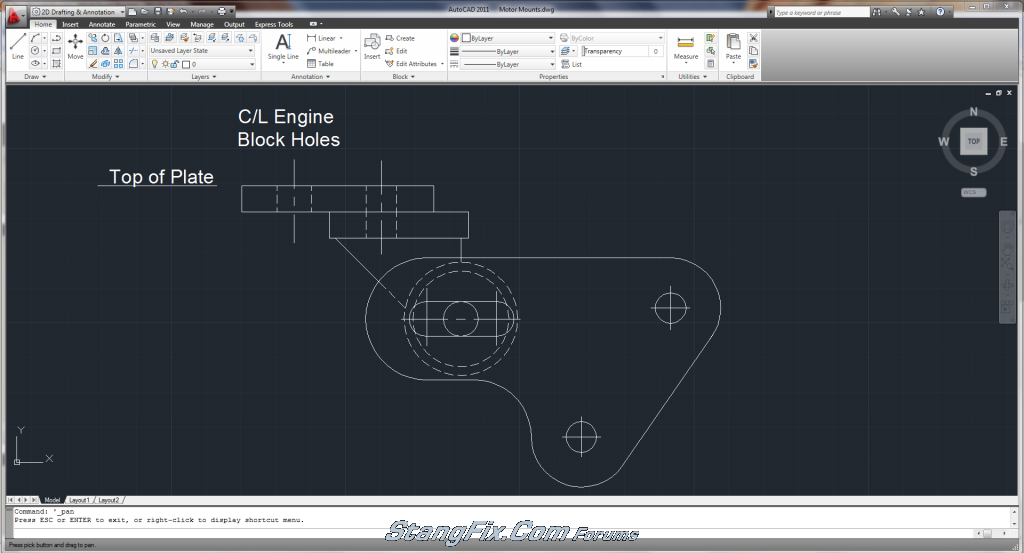
The above view is the completed side view of the motor mount assembly. This weekend I plan on drawing up the top view showing the width of the bushing, bushing housing, and details of the top plate and intermediate plate. I'm waiting on my rubber shackle bushings to come in the mail. When finalized, I will break up each part so that they can be transferred to steel plate to be cut. I plan on dimensioning everything and posting it on here so that other DIY guys can mimic my mounts...at your own risk of course :scar More to come later!
Oh, forgot to mention that when finished I'll be transferring these drawings onto cardboard for mock-up rather than going straight to cutting steel. Just in case something is off! :lol
Last edited by a moderator: