My father had a bunch of spare steel tubing and I needed a workbench, so I decided to work on my welding skills....trial by fire.I haven't done very good at taking pictures of my build, but here are a few I took tonight. It is overkill city, with 2"x2"x1/4" tubing that is 24" deep and 8' long. I decided to add interior legs as I didn't want a full 8' span on the tubing, plus it boxes in the roller cabinets on the ends. I still need to buy another roller cab. The open center area will house a stool or two. I am planning on using a steel plate top of unknown thickness yet, likely 3/16" or 1/4" unless I find a deal on plate steel. Below are a few in-progress pics
I do need some input though. I'm planning on using the receiver hitches at the upper corners of the open stool area to hold bench vise, bench grinder, etc. Which way would you have the tubes, with the welded ring hanging out past the bench (back of ring welded to upper bench tube, so it'd be pushed back as far as it'll go), or would you flip it around so that there is no ring and just weld it flush?? Below are a few pics of the two options. They are incorrectly placed at an angle due to clamping issues I had. Picture them not at an angle
Ring exposed:
No ring:
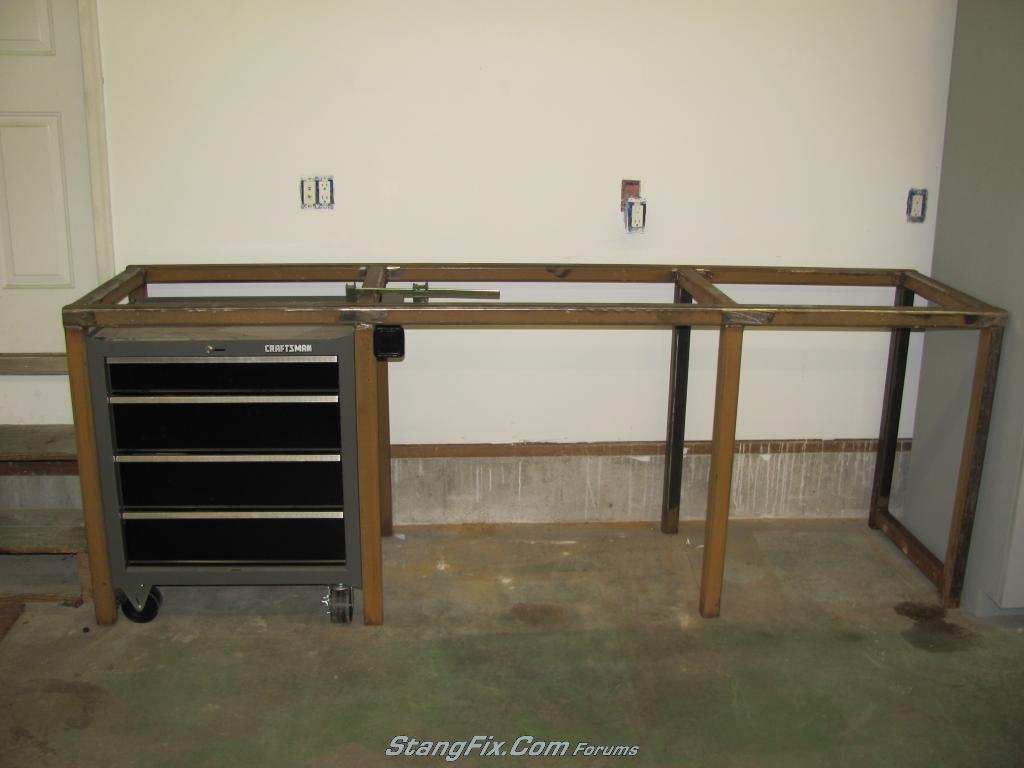

I do need some input though. I'm planning on using the receiver hitches at the upper corners of the open stool area to hold bench vise, bench grinder, etc. Which way would you have the tubes, with the welded ring hanging out past the bench (back of ring welded to upper bench tube, so it'd be pushed back as far as it'll go), or would you flip it around so that there is no ring and just weld it flush?? Below are a few pics of the two options. They are incorrectly placed at an angle due to clamping issues I had. Picture them not at an angle
Ring exposed:
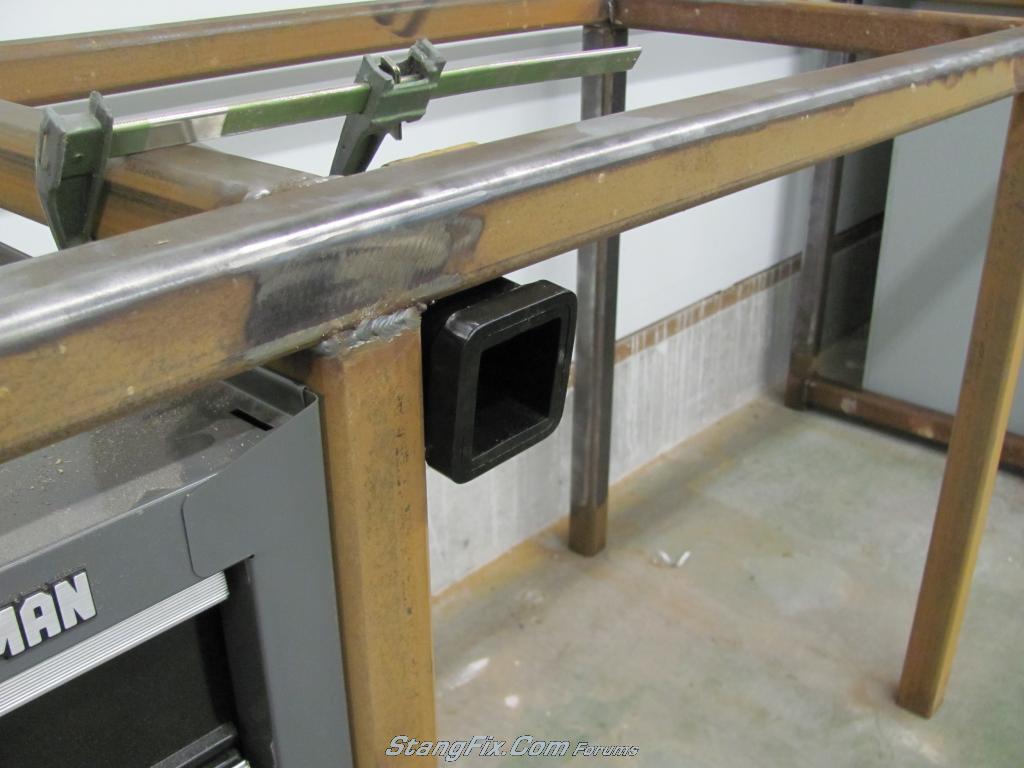

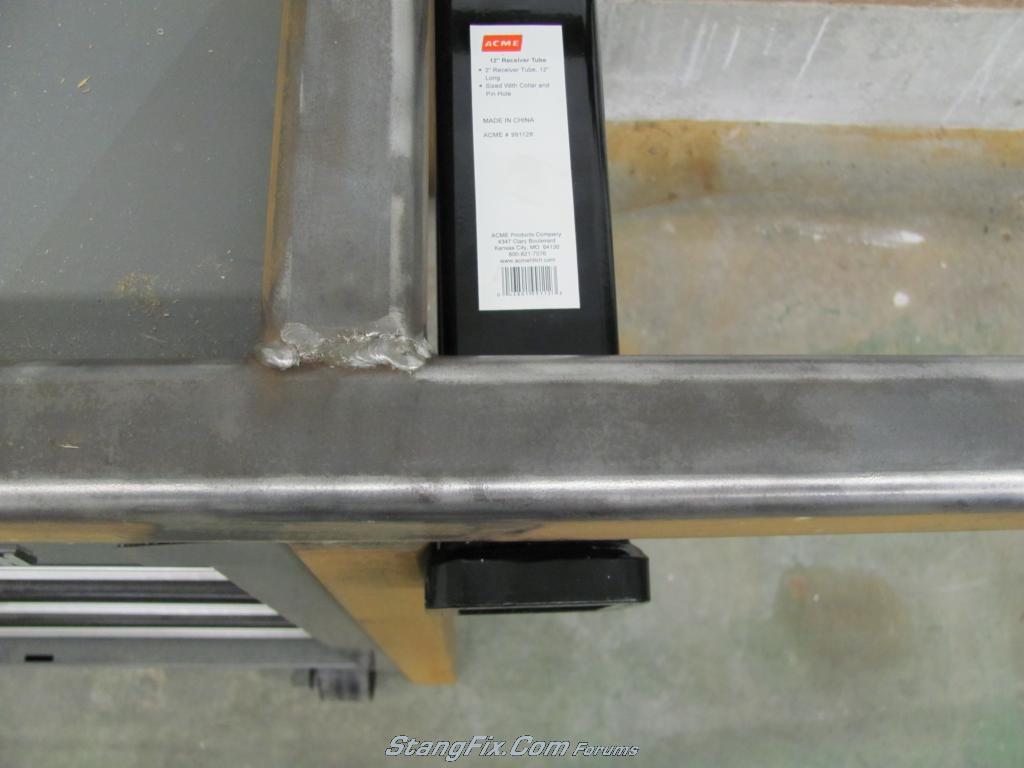
No ring:
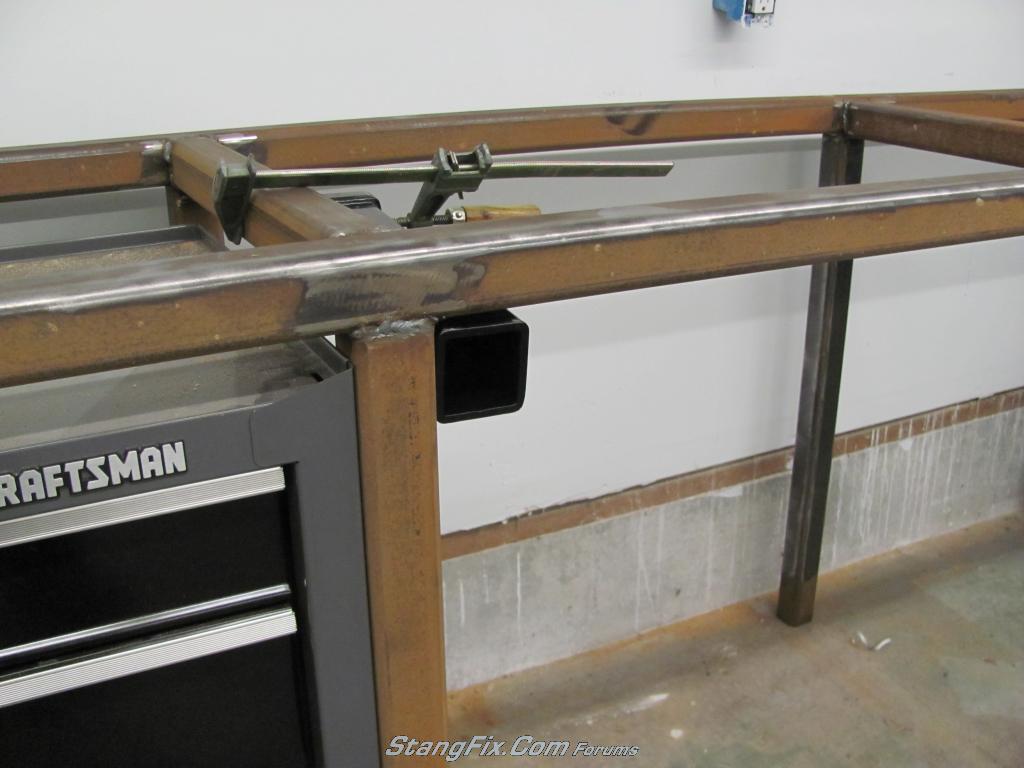
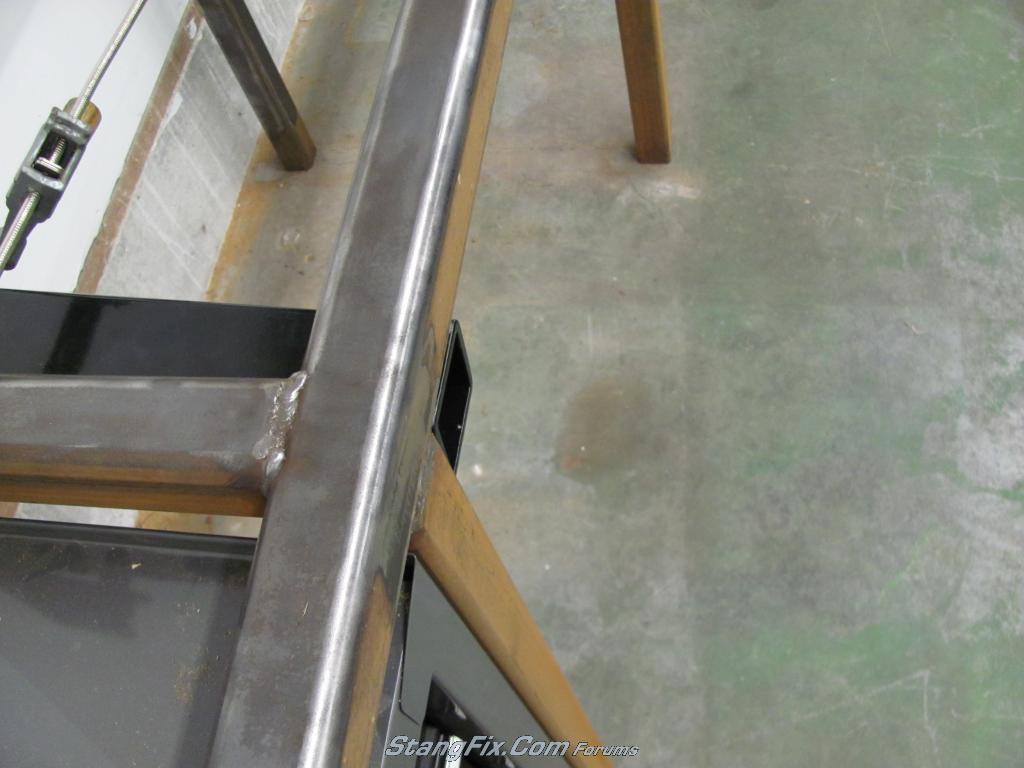
Last edited by a moderator: