WOW. Guess I haven't been here in a while. Have a lot of catching up to do but that will have to wait. I might actually get an entire day in the garage to day so going to take advantage. Need to fab up a tubing straightening tool so I can get at it on the fuel and brake lines. Also been chomping at the bit to try my hand at a fuel neck modification along the lines of Craig's but with a commercial piece I picked up to address the issue of gas spillage. And finally time to get going on installing this...
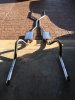
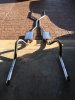