Back home finally and back in the garage. Pulled the two sections back together and made sure all was aligned and square. Ground a nice, even bevel on the edges and proceeded to weld it back together. First outside and then on the inside too. I ground most of the inside weld flush (left a bit of thickness on the underside of the top leg) so a plate would rest flat against the vertical rail side. Decided against reusing the old frame pieces for fish-plating the rails back together. Wanted something a bit thicker so I used some 3/16" cold rolled plate cut to size with the plasma torch. LOVING that thing. Fired up the MIG and burned it in all around. There were a number of unnecessary holes in the stock frame section that the fish-plate covered so I also did some plug welding on the other side to further mate the stuff together. Next I will be adding a boxing plate to the inside of the rail to totally enclose it and add some additional strength to the frame but before I can do that I had to weld in some nuts to the outer vertical rail section where a running board backet will mount. A couple of those bracket bolts go through the extra thickness of the plate which will only add even more rigidity to the board when stepped on.
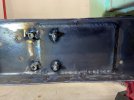
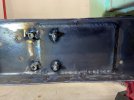