Well, that took a bit of nerve. Destroying a perfect 70 year old dash. Oh well. What's done is done. Time to move forward. Actually I was super anxious to cut into it to see how my measurements and handiwork on the even older donor dash worked out. Would it fit as planned?
Well, pictures tell the story they say.
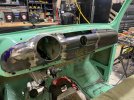
Have to say I am quite pleased with the fit.
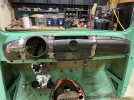
The way I cut it across the top worked out very well. I need to make that filler piece in the center which is fairly straight forward with just a slight curve to it both horizontally and vertically. Not too difficult at all. I think I can simply persuade the narrow panel above the glovebox to raise up just a bit to be in line with the existing dash and not even have to make a piece to marry that area. I was able to get the upper gauge pod to flow in really nice. Under the new dash section where I left most of the old dash lower edge is going to work out well too. I have something special planned for there and and additional lower section under it. That will come later.
Well, pictures tell the story they say.
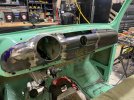
Have to say I am quite pleased with the fit.
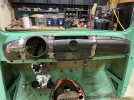
The way I cut it across the top worked out very well. I need to make that filler piece in the center which is fairly straight forward with just a slight curve to it both horizontally and vertically. Not too difficult at all. I think I can simply persuade the narrow panel above the glovebox to raise up just a bit to be in line with the existing dash and not even have to make a piece to marry that area. I was able to get the upper gauge pod to flow in really nice. Under the new dash section where I left most of the old dash lower edge is going to work out well too. I have something special planned for there and and additional lower section under it. That will come later.
Last edited: