Warning, if you see this guy with a welder in his hands, run for your life..........
....otherwise you might find him trying to burn down my shop at home or hopefully soon attempting to burn down his own garage.
Yesterday, Abe brought over his newly bought welder to my house to practice some welding. His machine is capable of doing both flux and mig welding. Currently it is set up as flux so we tried some welding on some text pieces. I have never done any flux welding and now I know why.
FLUX SUCKS
We practiced some spot welding after I drilled out some random hole in one of the test piece plates and no matter how both of us tried, we could never get a pretty weld. Major splatter, lots of smoke and fumes.
Flux 1
Flux 2
I finally said "Flux this" and pulled out Mr. Miggy, my mig welder. I did one spot weld and then gave the gun to Abe who filled in the remaining 9 holes:
Mig 1
Mig 1 backside
Hopefully this exercise has convinced Abe to switch his machine over to Mig.
....otherwise you might find him trying to burn down my shop at home or hopefully soon attempting to burn down his own garage.
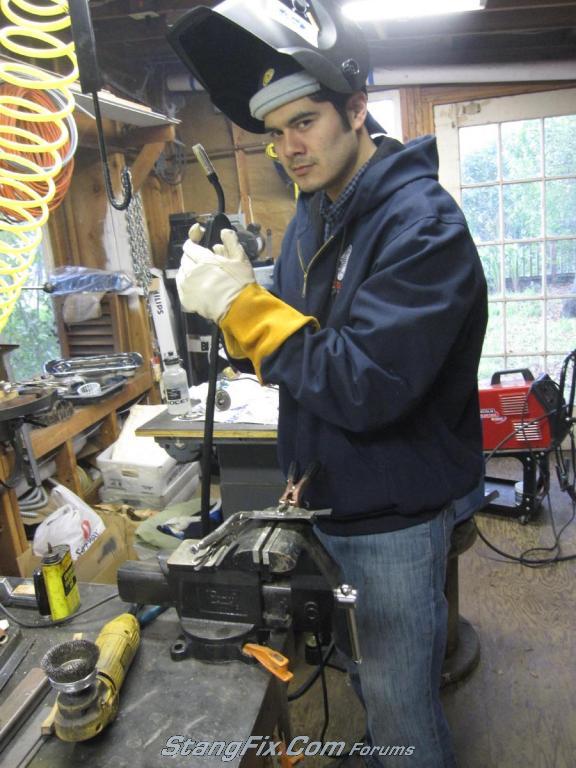
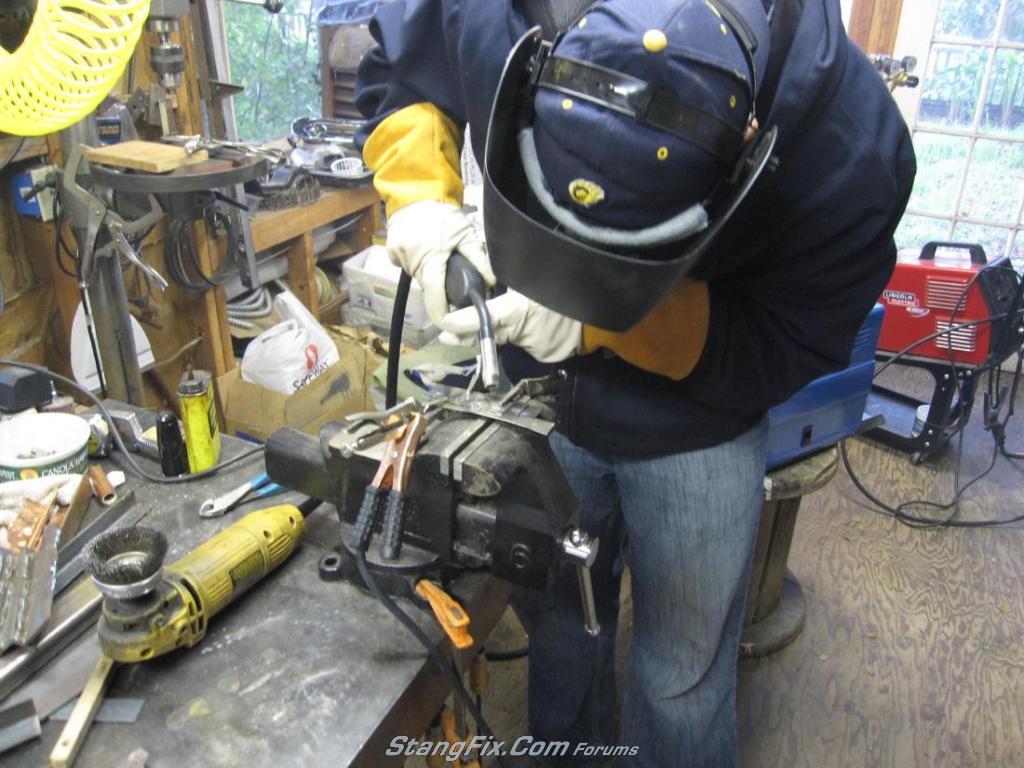
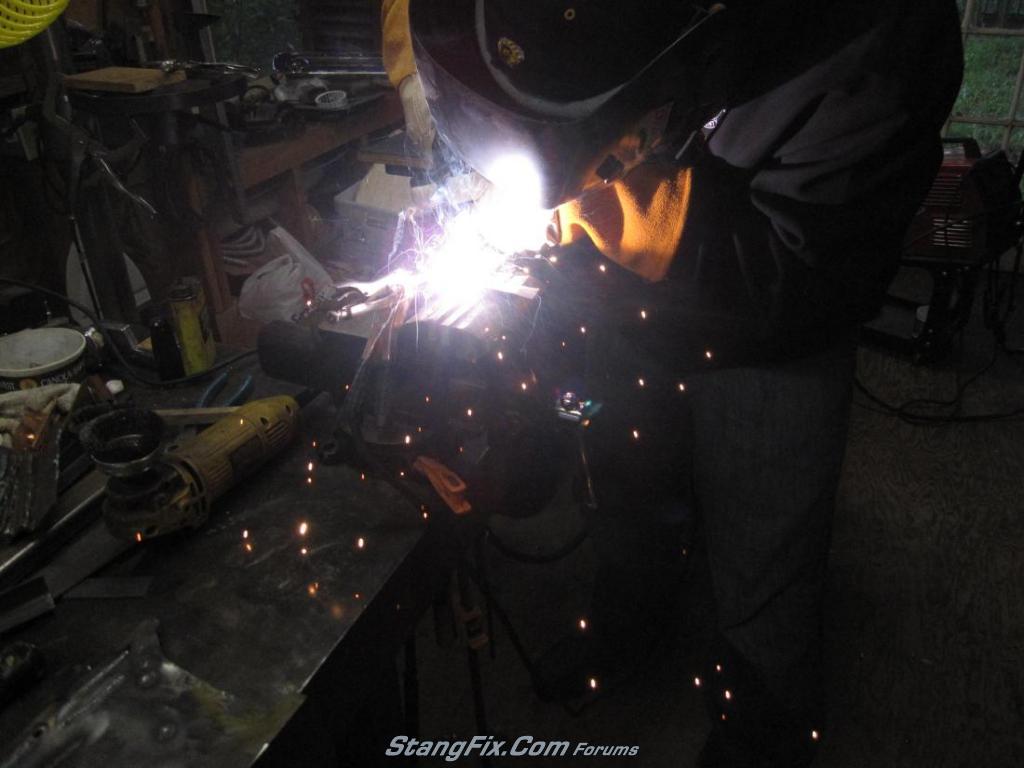
Yesterday, Abe brought over his newly bought welder to my house to practice some welding. His machine is capable of doing both flux and mig welding. Currently it is set up as flux so we tried some welding on some text pieces. I have never done any flux welding and now I know why.
FLUX SUCKS
We practiced some spot welding after I drilled out some random hole in one of the test piece plates and no matter how both of us tried, we could never get a pretty weld. Major splatter, lots of smoke and fumes.
Flux 1
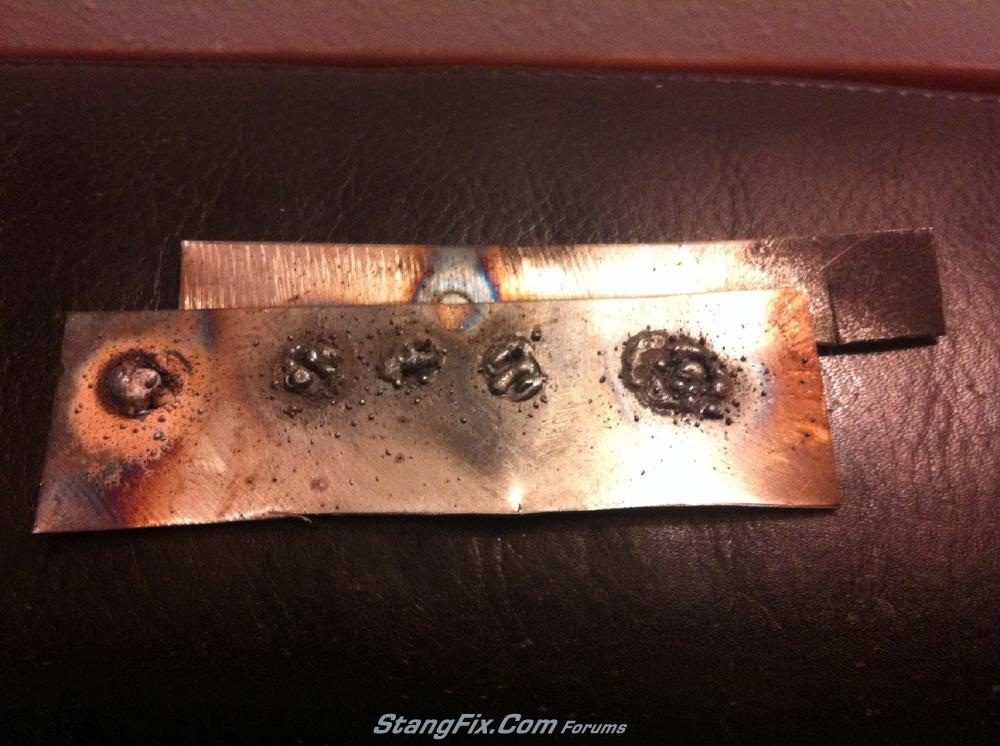
Flux 2
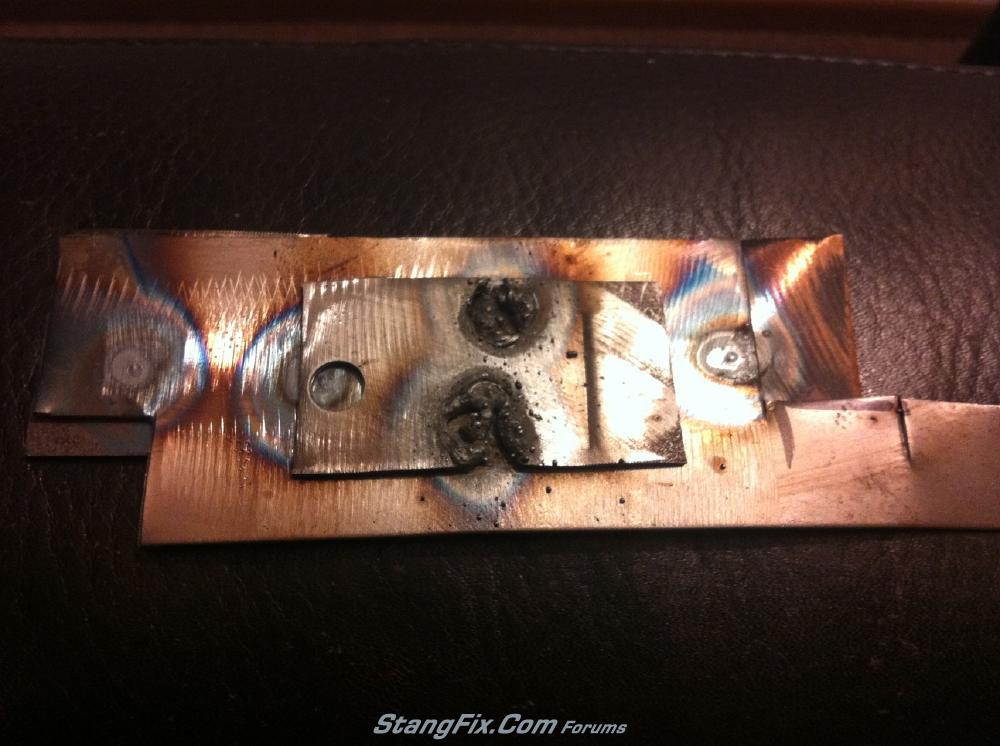
I finally said "Flux this" and pulled out Mr. Miggy, my mig welder. I did one spot weld and then gave the gun to Abe who filled in the remaining 9 holes:
Mig 1
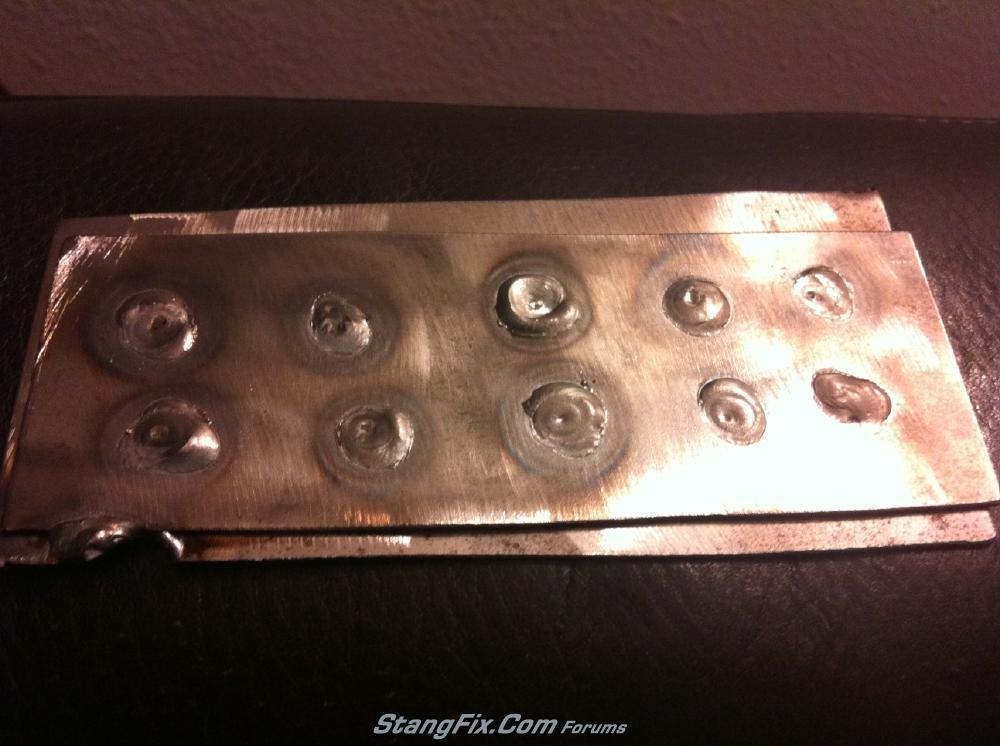
Mig 1 backside
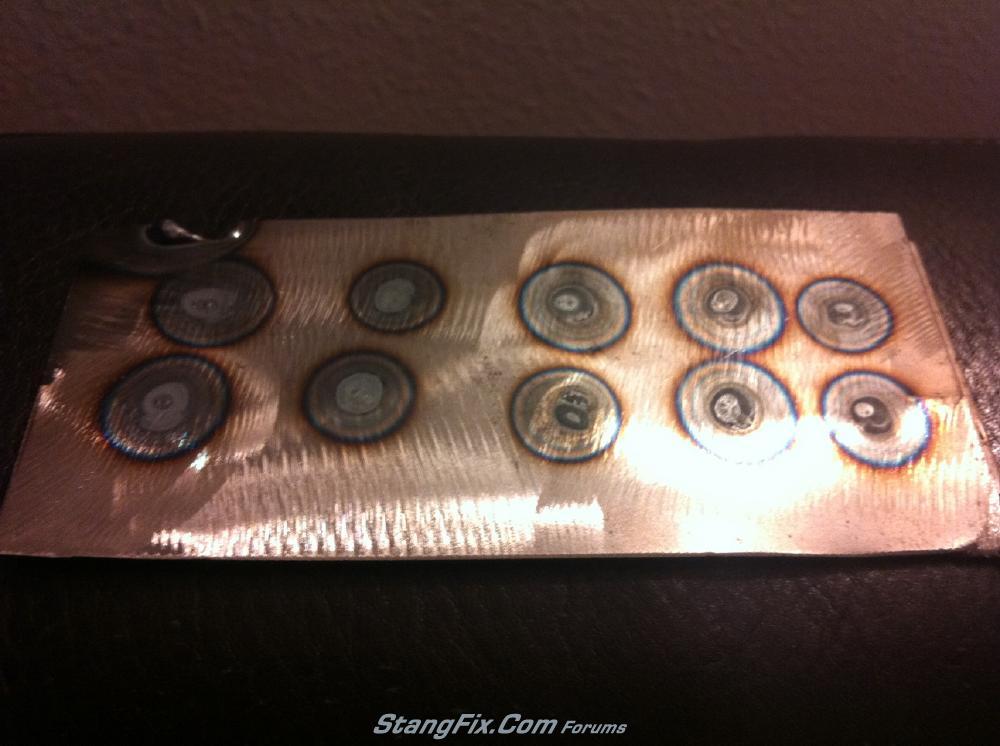
Hopefully this exercise has convinced Abe to switch his machine over to Mig.
Last edited by a moderator: