JRANGER
Active Member
Well im officially starting on my 65 project. I hope to make this an Eleanor so i should add a lot of MTF stuff to her once i get into that phase
Coupe is solid, will prob need front floor panels and some trunk metal. Rear already converted to 5 lug and a 8" With new leafs. Has sub frame connectors and torque boxes to install
Have all parts for v8 swap front, granda spindles/disc setup, and new front suspension to install as well as manual steering v8 parts (The front suspension will prob change as im thinking about some form of coil over and EPS)
Anyway, ive torn the whole interior out, removed the qtr windows, pulled the tank, railights, and qtr extensions out.
Now to start bracing her up from cutting
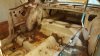
Coupe is solid, will prob need front floor panels and some trunk metal. Rear already converted to 5 lug and a 8" With new leafs. Has sub frame connectors and torque boxes to install
Have all parts for v8 swap front, granda spindles/disc setup, and new front suspension to install as well as manual steering v8 parts (The front suspension will prob change as im thinking about some form of coil over and EPS)
Anyway, ive torn the whole interior out, removed the qtr windows, pulled the tank, railights, and qtr extensions out.
Now to start bracing her up from cutting
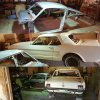
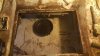
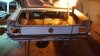

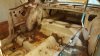