chaser012001
66 408w, TKO600 coupe...in progress
Oh man I'm getting way behind in my posts!
I received the shipment from SoT a few weeks back. It was a delivery of 6 boxes of joy...that was blocking my wifes side of the garage so I had to quickly get things move before she got home, i digress.
Opening these things was like getting a late Christmas! I opted to go with the frame mount watts link, full floating housing, 31 spline axles, and 11.75" disc brakes. For those that dont know, there are two different mounting types for the watts link; leaf mount and frame mount. Shaun explained that the leaf mount is perfectly fine for folks who dont ever intend to put mini-tubs in but will interfere with the tire if you do. The frame mount, while a little more difficult to install since welding is involved, moves the trailing arms more inward thus, mediating the potential clearance issues. I dont know if I'll ever put tubs in the car but wanted the option...and i dont have issues welding. Thats why I went with the frame mount.
TOYS:
The provided instructions are pretty good and easy to understand...and everything would have gone great save for a couple minor issues. The first being that, over the years I had replaced the rear portions of the frame rail. As luck would have it, the welded joints were right over where the watts link frame was going to mount and it wouldnt slide over. No worries, I ground the welds down a little and we were in business! NOTE: back in the day when I replaced those rails, I fish-plated the inside as well to add reinforcement.
The other, more annoying issue, was that I replaced the drivers torque box with a convertible box which then kinda messed up the measuring points as I found AFTER i had tacked everything in. Which leads me to words of wisdom: tack and test fit your parts BEFORE final welding kids...
There I was, admiring my handywork when I noticed the rear was slightly more aft on the drivers side than the passenger. A couple quick measurements confirmed that they were off almost an inch from eachother...not good.
This is where I stopped and started trying to understand what had happened. It also ended with another call to Shaun to get his opinion on what would be the best approach which was inline with what I had though...i also wanted to order the center section :-D
Next post as this gets kind of lengthy...
I received the shipment from SoT a few weeks back. It was a delivery of 6 boxes of joy...that was blocking my wifes side of the garage so I had to quickly get things move before she got home, i digress.
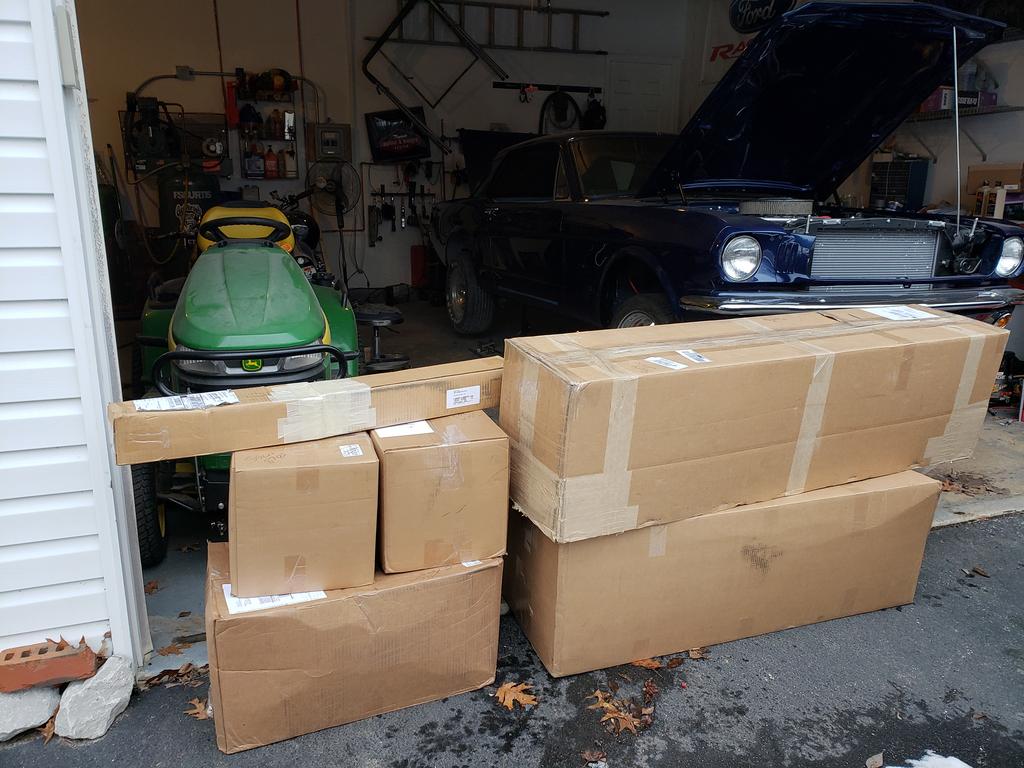
Opening these things was like getting a late Christmas! I opted to go with the frame mount watts link, full floating housing, 31 spline axles, and 11.75" disc brakes. For those that dont know, there are two different mounting types for the watts link; leaf mount and frame mount. Shaun explained that the leaf mount is perfectly fine for folks who dont ever intend to put mini-tubs in but will interfere with the tire if you do. The frame mount, while a little more difficult to install since welding is involved, moves the trailing arms more inward thus, mediating the potential clearance issues. I dont know if I'll ever put tubs in the car but wanted the option...and i dont have issues welding. Thats why I went with the frame mount.
TOYS:
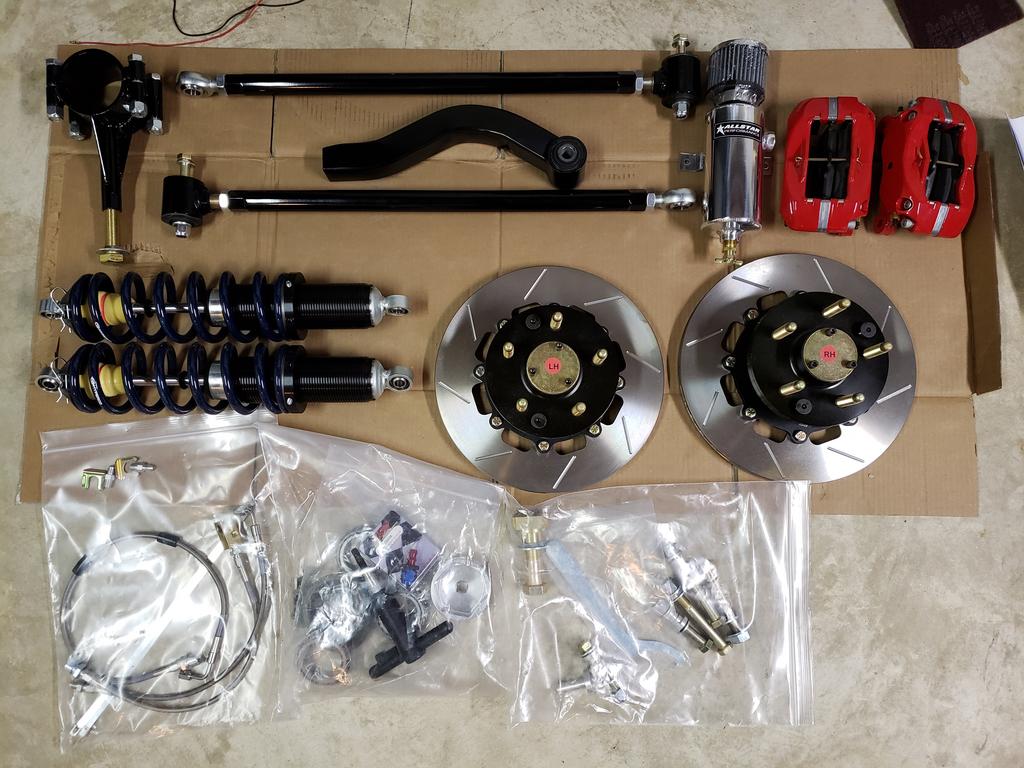
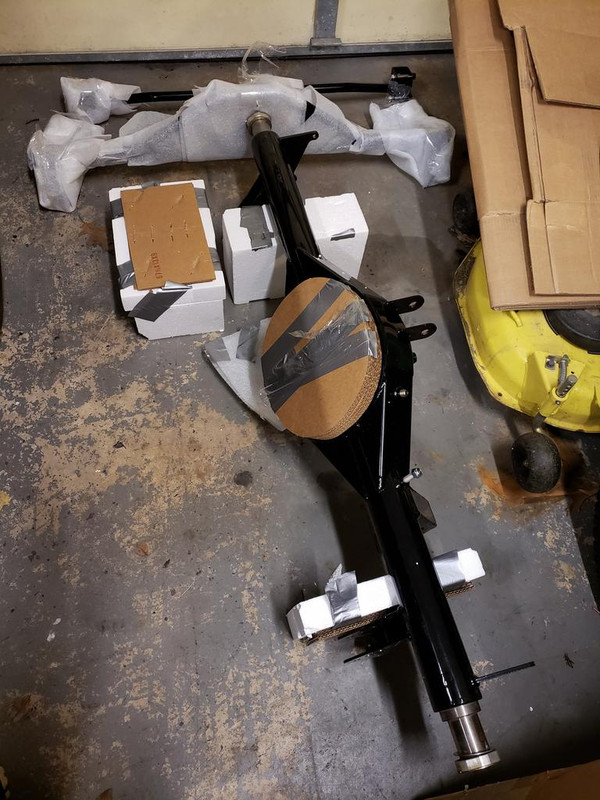
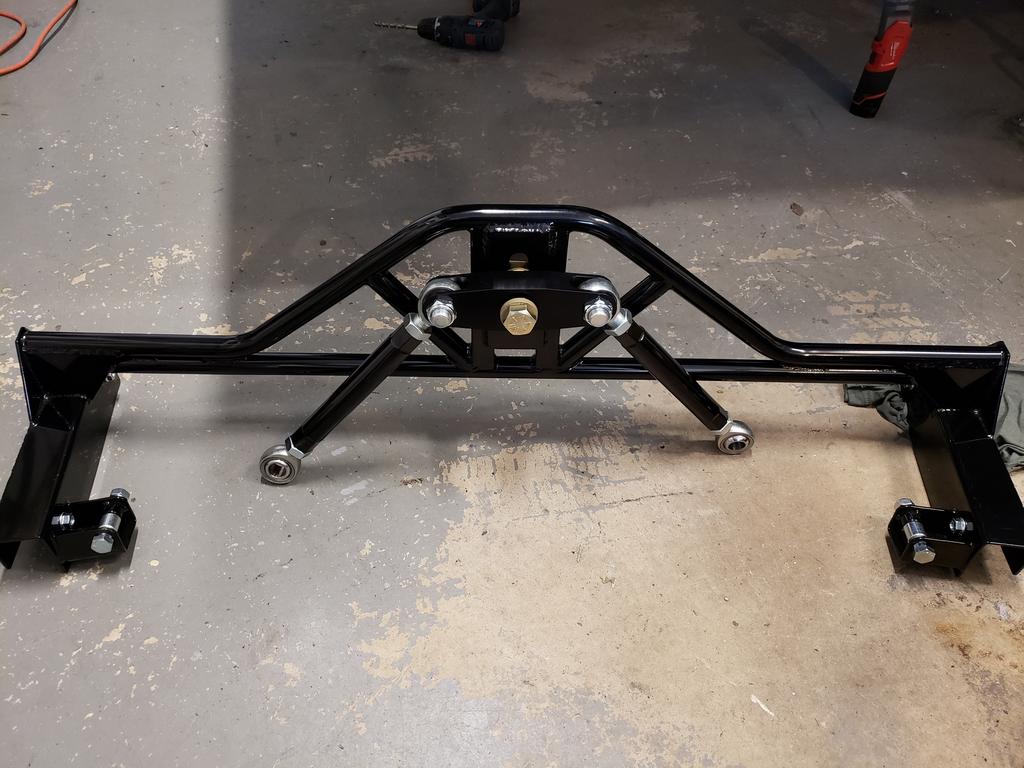
The provided instructions are pretty good and easy to understand...and everything would have gone great save for a couple minor issues. The first being that, over the years I had replaced the rear portions of the frame rail. As luck would have it, the welded joints were right over where the watts link frame was going to mount and it wouldnt slide over. No worries, I ground the welds down a little and we were in business! NOTE: back in the day when I replaced those rails, I fish-plated the inside as well to add reinforcement.
The other, more annoying issue, was that I replaced the drivers torque box with a convertible box which then kinda messed up the measuring points as I found AFTER i had tacked everything in. Which leads me to words of wisdom: tack and test fit your parts BEFORE final welding kids...
There I was, admiring my handywork when I noticed the rear was slightly more aft on the drivers side than the passenger. A couple quick measurements confirmed that they were off almost an inch from eachother...not good.
This is where I stopped and started trying to understand what had happened. It also ended with another call to Shaun to get his opinion on what would be the best approach which was inline with what I had though...i also wanted to order the center section :-D
Next post as this gets kind of lengthy...