A
Anonymous
Guest
Abe, take a look again at some of J's welds and compare then to what you've done. I hate to say this, but Mid seems to be on the right path. The welds would lay flatter if your temps were hotter. Are you pushing or pulling the puddle?
Compare these welds to yours.
Compare these welds to yours.
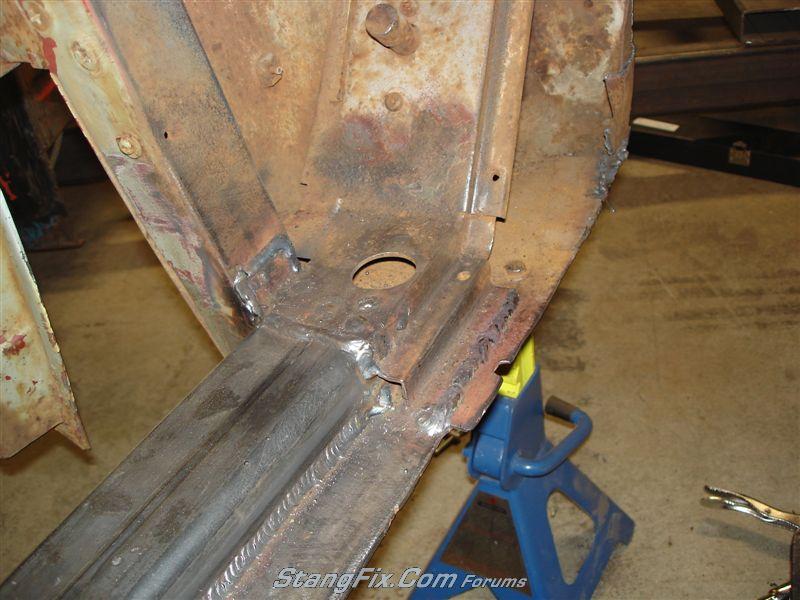